The
facility, shown below, is quite large. A
schematic illustrates the important dimensions and rough
layout of the device. The large white tank in the photo above
is the supply section. The tank is filled with tap water, while
a thick (50% by volume) slurry is fed from the platform above
through a small tube to the bottom of the tank. Due to the many
bends in the inlet pipe, the slurry is well-mixed when it enters
the larger tank (shown empty above, though it is filled to the
brim when a fan is being built).
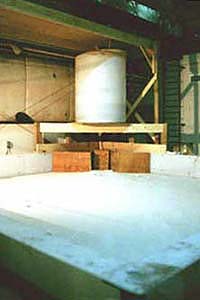
One the biggest problems forming a realistic fan is that the
flow coming out of our source must be a plume (a buoyantly-driven
flow), and not a jet (an inertially-driven flow). That is the
reason for the equilibration section shown in the
schematic.
In fact, we also have a turbulence-dampening arrangment which
keeps the particles entrained while reducing the interia and
turbulence in the entering flow. The arrangment consists of
a box with holes drilled on both in the inlet and exit side
in random locations. Within the box, styrofoam peanuts nearly
fill the entire volume. When the dense, sediment-laden fluid
flows in the peanuts move around keeping the sediment fluid
mixed, while removing much of the energy. The result is a flow
which transitions to plume within 10-20 cm of the box exit.
Finally, we need a way to remove the current to prevent it from
reflecting of the far walls and reworking the deposit. Most
experimentalists make this space too small, but we found the
0.5 m space usually just enough to eliminate reflection. Reflections
are also prevented from an exit pipe placed on the floor of
the tank with appropriately drilled holes to ensure equal removal
of dense fluid.
Generally our fans
are made of Balotini, a type of blown silica used in sandblasting
equipment. The material is cheap (less than a quarter per kg)
and easily accessible. It is also highly spherical (due to its
formation process) and can be obtained in highly well-sorted packages.
Typically, the Balotini has a mean diameter of around 40 microns.
Variations within each batch allow us to visualize where both
the coarse and fine portion of the current is deposited.